Le CETIA révolutionne le recyclage textile
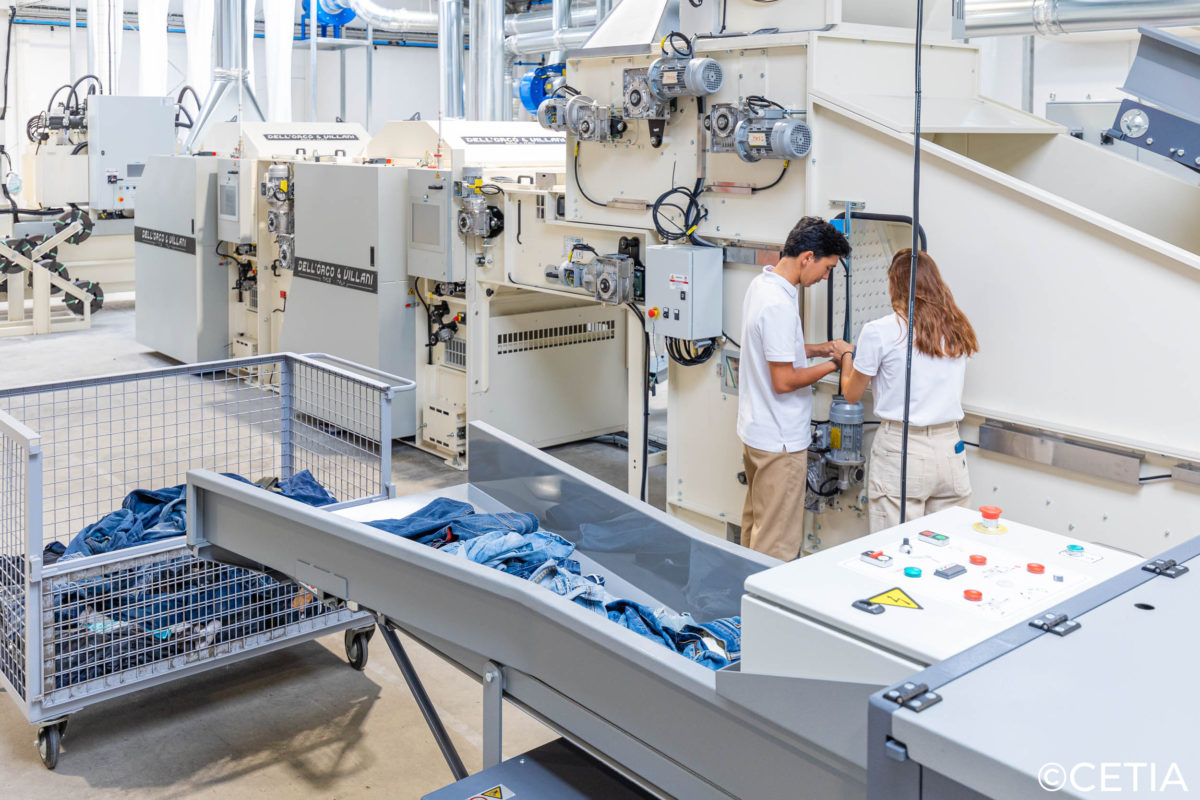
Crédit : CETIA
Le 6 septembre 2023, le CETIA, une plateforme d’innovation dédiée à la recyclabilité textile, a inauguré ses nouveaux locaux de 1200 m2 à Hendaye (64). Explications avec la directrice de cet acteur innovant, Chloé Salmon-Legagneur.
Comment le CETIA a-t-il été créé et dans quel but ?
On a démarré des réflexions autour du projet du CETIA en 2019, dans le cadre de la chaire BALI (programme de recherche et d’innovation créé en 2017 réunissant des acteurs du textile – ndlr). Dans ce cadre, l’école d’ingénieurs ESTIA, depuis 2017, travaille avec des industriels de la mode, notamment Décathlon, Petit Bateau, le Groupe Eram, le CETI (le Centre européen du Textile Innovant), Belharra ou Rediv, sur comment l’innovation peut accompagner l’industrie de la mode et du textile dans sa transition sociétale, environnementale et économique. Dès 2019, le CETI a expliqué que si on veut faire de la matière recyclée à grande échelle, on va buter sur la partie identification et démantèlement des vêtements. Aujourd’hui, les produits recyclés sont majoritairement faits avec des chutes de production. Pour changer d’échelle, il faut des gisements supplémentaires. Les opérations de tri et d’identification étaient souvent manuelles, et l’ESTIA qui travaillait beaucoup sur la robotique, l’automatisation et commençait à travailler sur l’intelligence artificielle a proposé d’amener de la compétence pour que ces opérations puissent être automatisées. Les marques ont souhaité financer ces programmes et la région Nouvelle-Aquitaine a proposé de co-financer les équipements. Dès fin 2019, la région a investi 700 000 euros pour financer 1,4 million d’euros d’équipements. Cela nous a permis de passer de l’idée à la réalité. Le CETIA a été créé en 2021, avec deux actionnaires : l’ESTIA et le CETI.
Pouvez-vous nous en dire plus sur ces manques dans la chaine du recyclage textile ?
Quand on veut recycler des vêtements, il faut avoir isolé l’ensemble des matières. La filière est dépendante des solutions de recyclage développées. Le jean par exemple, on sait en faire du métisse, un isolant pour la maison. Et de nombreuses start-ups ont été créées sur des typologies de matière ; une société finlandaise a mis au point un système pour recycler le coton mais il faut plus d’un certain pourcentage de coton, d’où le besoin d’identifier complètement la matière ; en France, on a Carbios, qui recycle le polyester avec un procédé enzymatique très vertueux. Il faut donc qu’à un moment dans la chaine de recyclage, on identifie la composition d’un vêtement pour l’orienter vers la bonne solution, sachant que les étiquettes sont souvent coupées quand les vêtements ont été portés. Et quand on a identifié la matière, il faut pouvoir supprimer les points durs (zips, boutons, étiquettes…) Tout dépend du cahier des charges du recycleur. Ce sont souvent des opérations manuelles qui ont permis de faire de premières réalisations, mais pour changer d’échelle et recycler en quantité on ne peut pas rester sur ces opérations manuelles ; ça ne permettra pas à la filière de se développer.
Changer d’échelle, c’est ce qui est expérimenté au CETIA ?
Ce qu’on cherche à faire, c’est à automatiser le plus possible ces opérations dites de préparation de la matière au recyclage. On travaille sur toutes les technologies qui peuvent nous permettre de collecter de l’information sur un produit et de l’identifier automatiquement. On travaille aussi sur ces sujets de démantèlement : comment isoler les boutons, zips, pièces métalliques, les parties textiles… On a fait l’acquisition d’une très grosse machine qui permet de faire ça, de passer jusqu’à 600 kg de vêtements à l’heure. La machine vient frotter le vêtement avec de gros rouleaux et pics, pour avoir en sortie un effiloché, donc de la fibre, dépourvue de tout point dur. En amont de cette machine, on a mis une machine de tri (FibrerSort) qui permet d’identifier les compositions des textiles. Cela permet d’envoyer aux recycleurs des volumes plus importants de matière. On travaille aussi sur des programmes d’innovation. On a travaillé sur une machine pilote pour les chaussures, afin de séparer automatiquement les semelles de chaussures, que l’on a fait cofinancer par différents acteurs (dont Zalando, Eram et Décathlon) qui souhaitent refaire des semelles à partir de semelles usagées. On a maintenant un outil qui permet de séparer 120 chaussures à l’heure (à l’échelle de pilote) pour les chaussures collées, et on va recevoir d’ici un mois une nouvelle technologie qui va nous permettre de découper les semelles lorsqu’elles ont été cousues, et injectées. Aujourd’hui, de nombreux acteurs ont vraiment cette volonté de réutiliser les matières qu’ils ont pu mettre dans leurs produits fabriqués et d’essayer de les collecter pour les réinjecter dans leur industrie. C’est au sein de la chaire BALI que l’on a ces réflexions : ce qu’on veut faire, comment structurer la circularité, de quoi les entreprises ont besoin pour se mettre en conformité avec la législation ou pour répondre aux besoins du consommateur ? Et ces réflexions nous amènent à réfléchir à de nouvelles solutions.
Vous avez communiqué sur un nouveau programme d’innovation avec « Refashion » ?
Refashion, l’éco-organisme qui finance régulièrement des programmes d’innovation a confié au CETIA un programme avec un engagement de 900 000 euros sur trois ans pour travailler sur des sujets d’innovation. Notamment sur la chaussure, on va essayer de mettre au point un système pour les saisir automatiquement dans un bac et les placer sur la ligne de démantèlement. On va travailler aussi sur comment aller au bout de la préparation de la semelle, c’est-à-dire quelle solution de broyage est la plus intéressante. On compte également étudier les différents capteurs du marché pour avoir de l’information sur les vêtements.
À lire aussi :
Comprendre : les impacts de l’industrie textile sur la planète
Le gouvernement veut aider à la réparation des produits textiles
Soyez dans le vent 🍃 :
Abonnez-vous gratuitement à la newsletter de Deklic en cliquant ici